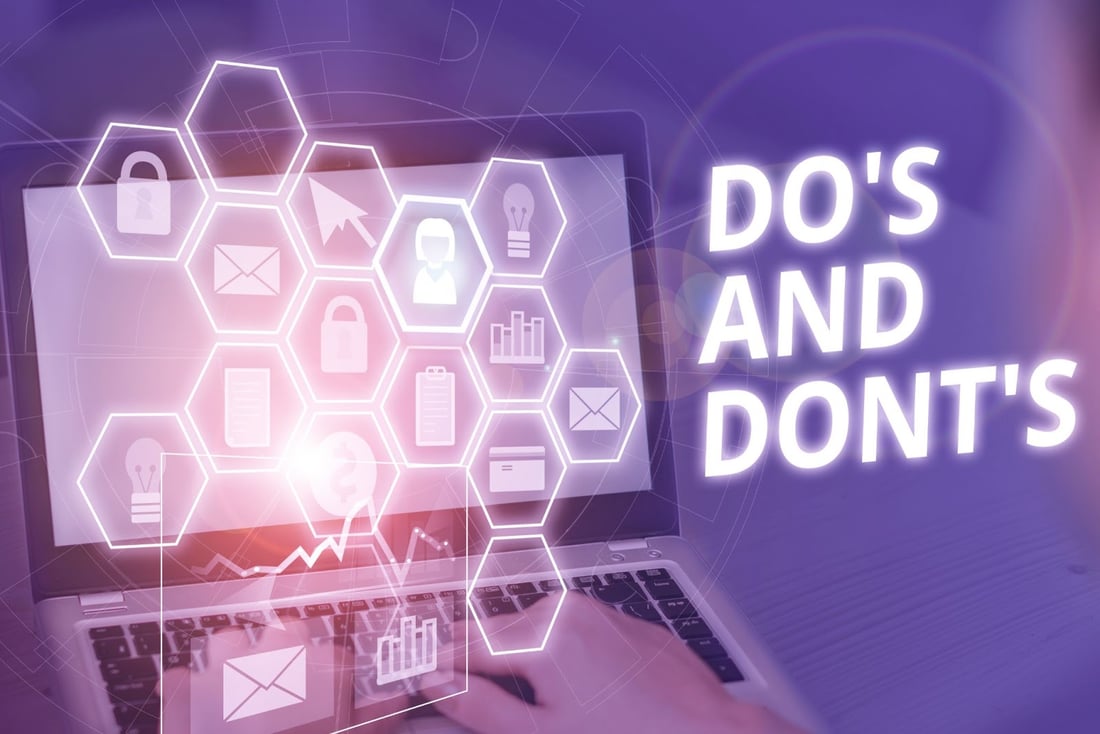
Considering the fact that less than 1% of the total material handling equipment is automated, adopting robots for load movements is still a “newer” approach for most warehouses.
With technical advancements and multiple iterations, innovative companies today can ensure a hassle-free (think infrastructure-free) installation and robust operations. While robotics can potentially reduce the time and costs in warehouse operations, adopting best practices and post-installation optimization is equally crucial.
Before deep diving into the specifics of your robotic project, a simple checklist to see if you are ready for automation? can come in quite handy.
Like any quantum leap, warehouse automation is a big step forward for your company, and care should be taken if both the warehouse and the company are sufficiently prepared for a move.
While a once in a blue moon event like suez canal traffic can affect warehouses, these are almost out of your control. However, by enabling industry 4.0 practices, the productivity in your warehouses can not only remain at an optimum level, but also offset external factors to an extent.
These do’s and don’ts can help you shape up your groundwork and identify the problem to be solved.
Do’s
1/ Study the expected ROI
Robotic trucks consist of a higher initial investment, but can break-even at a remarkably quick time. While estimating your expected savings, keep in mind that not-only are you achieving a higher efficiency but also possibly help your productivity. Reduction in goods damage, accidents and savings in time are also additional factors which help your operations.
Before these robots hit your warehouses, you should ideally know what you are saving and how much you are saving. If you are unable to get an estimate, our ROI calculator will prepare you in under 5 minutes.
2/ Automate processes that has a domino effect
Knowing which processes to automate can go a long way in determining the success of your automation process.
Simple and repetitive tasks are a good place to start your automation journey as you can relieve your operators from doing low-value added tasks and train them elsewhere.
However, automating processes that affect your other functions within the warehouse is of paramount importance. For example, not automating a material flow where there is a slowdown of load movements ( due to variable reasons like lack of operators / general mission delays) from station 1 to station 2 would mean an unnecessary hold-up in your overall productivity that would still persist if you neglect them.
Hence, in addition to keeping your first tasks simple, focus on automating tasks that would yield maximum output.
3/ Learn from innovators and competitors
It goes without saying that you will naturally grow studying the industry or even your competitor’s evolution. Not necessarily adopt the same practices, but to identify the type of operations that would add value to your material flows.
Industry leaders are often early adopters of technology, and achieving competitive advantage through automation is a great bet. Leaders in automobile, 3PL/distribution centers and E-commerce giants have become efficient by embracing robotization.
4/ Identify robots that compliment your existing operations
A pivotal factor is to identify robots that go well with your existing operations.Robots or traditional AGVs that require a path-following infrastructure like reflectors, wire guidance should be avoided in today’s operating environment as they are rigid and generally will not complement most warehouse ecosystems.
Geo-navigation robots, for example, are infrastructure-free, integrate seamlessly with WMS/ERP systems, automatic doors and in case of third-party logistics, conveyors and stretch-wrappers without the need for any additional infrastructure.
Don’ts
1/ Labor misallocation
By considering automation, care should be taken that you embrace the notion of ‘cobotics’- where humans and robots coexist and work together. Remember : autonomous robots are not here to replace your existing manpower, rather work with them and take over their low-added tasks, freeing them to focus on creative or high-value added tasks.
By replacing entire manual labor with robots, efficiency of material handling will increase but the overall plant efficiency would not necessarily increase. Labor misallocation is one thing emerging companies need to take note of. Autonomous robots require minimal human oversight, but work best when deployed in an inclusive setup.
2/ Trend > Suitability
Mobile robots or autonomous high-lift robots? Even if you choose one, there are multiple options depending upon load capacity and other technical factors.
One thing that needs to be avoided is to go only with industry trends and consider adopting robots that are either not suitable or do not solve the primary pain point. For example, a typical warehouse move pallets horizontally and vertically, and autonomous robots that can do both are your ideal solution. Automating warehouses can be a game-changer and identifying the right robot for your needs is decisive.
Hint : If you are looking for a solution provider who can help you optimize your operations and suggest suitable robotic trucks, consider suppliers who have a broad portfolio both with product range and client testimonials.
3/ Neglect post deployment optimizations
The final stage of automation is not deployment of robots, in fact that’s only the final stage of your project.
However, in order to reap the rewards of automation, regular optimization and analysis should be done to ensure you are in sync with your KPIs. Care should be taken that conditions in the warehouse remain favorable for operating your robots, even if there is a change in material flows. Under optimal conditions, performances of autonomous robots can be profitable and provide grounds for future scalability.
When it comes to increasing productivity and operational efficiency, your success boils down to 2 things : The robots you choose and the level of integration you can manage to achieve.