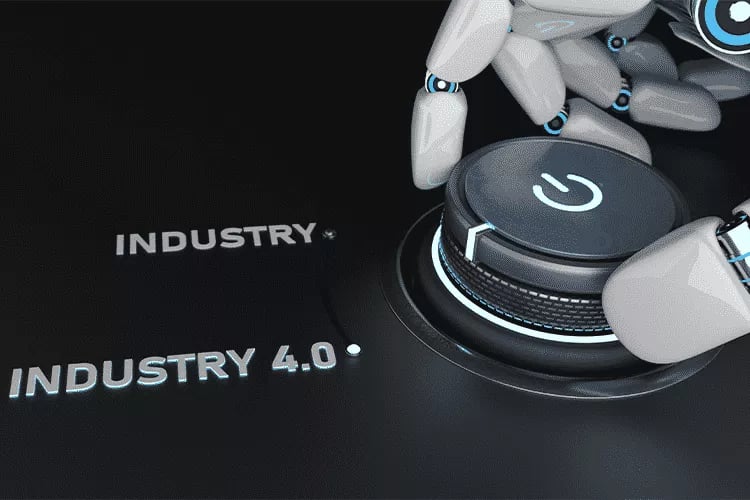
You have decided to automate your pallet transport, Great! Now you have to look for an effective solution before looking for service providers. Should you implement an AGV system, conveyors, or other fixed systems? How easy (or otherwise) would the installation be? Which one should you look at? Here are some key points which might help you.
Ease Of Installation
Any operational warehouse looking to revolutionize the goods transfer process will look for an automation system that is easier and cost-effective to implement. This puts an AGV system at an advantage over a fixed automated system like conveyors. With an AGV, you don’t need to redraw or move your existing operation lines.
Another point is the time consumed to install these systems. An AGV is quick and easy to install and does not interfere with ongoing production or warehouse processes. A fixed automation system can often be time-consuming, and in some cases, requires a partial adjustment of operations.
Maintenance & Energy
One benchmark of an automation system is the potential return on investment, which makes maintenance a crucial driving factor. With minimal maintenance requirements and advanced energy solutions, the maintenance cost of an AGV is much lower as compared to the conveyors. Conveyors, although helpful in goods transfer, require a constant and costly maintenance schedule to keep it operational. This takes us to the second point: power consumption. AGVs use (battery) power on demand, directly correlating to the warehouse load, while a conveyor system uses constant power for all types of operations, thereby increasing the energy cost.
Flexibility And Scalability
Lean Manufacturing is the ideal practice production factories chase and implement. This makes any potential new system consistent with existing practices. Again, an AGV may be chosen over fixed systems for its ease of flexibility and scalability. An AGV system does not need changing production routes since it does not occupy a fixed space. Fixed automation, especially conveyors, takes up substantial space, which can hinder certain movements around the plant and thereby decrease the throughput. Furthermore, when the conveyor stops, other logistics flows get hindered as well. In cases of scalability in the future, an AGV is your best bet as any new potential increase in requirements can be handled by simply deploying additional trucks. Conveyors, in this regard, are limited to short load transfers and a maximum throughput threshold.
Market Trends
The global AGV market size is slated to exhibit a CAGR of 9.5% by 2025 against 4.5% for conveyors. Automation in industrial processes is primarily based on the integration of the Internet of Things (IoT) with the existing infrastructure. AGVs are a forerunner to the adoption of technologies in any industry.
* Note : AGV = Autonomous Guided Vehicles