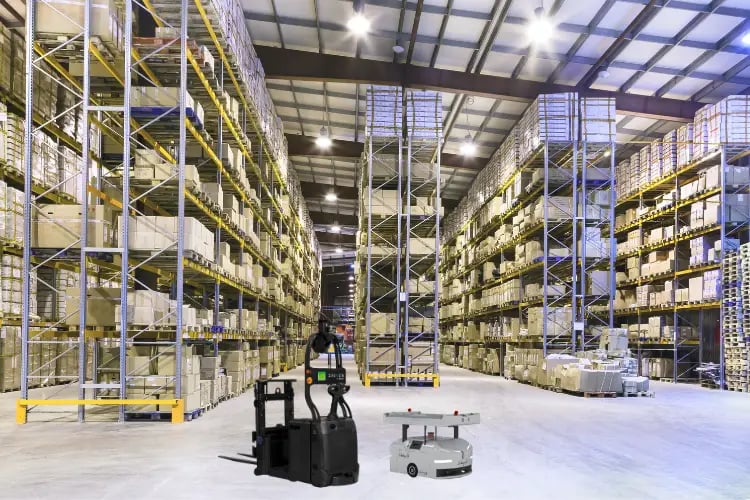
Automating internal supply chain or logistic flows is always a challenge for both big and small companies. With more and more sophisticated systems, companies are increasingly looking to replace operator dependency and let robots handle the goods transfer activity. Two automation systems are customer’s go-to option for goods/pallet movement: AGVs and AMRs. While AGVs have been around for a long time, drastically increasing their functionality and technology over time, AMRs are gaining traction in recent times.
However, for companies who are looking to not only automate but also potentially increase their productivity by retraining the operators to do more value-added tasks, a complete load handling capability and adaptability is essential. Hence, an AGV is an attractive proposition to look at.
But how are they different from AMRs?
Load Handling Capabilities
AGVs and AMRs vary in terms of the capacity and type of load transfer they are deployed for. AGVs can be used to handle pallet loads for both horizontal and vertical applications, whereas AMRs are used for floor level movements only. Although AMRs are flexible and fluid, they would not be completely efficient should you need to store/retrieve pallets from elevated racks. Another factor to consider is the maximum weight of the load. AMRs are generally efficient and feasible for loads less than 200kgs. For load movements over 200 kgs, an AGV is your best bet since they can safely handle up to 2000 kgs.
Dual-Mode
Another crucial difference between AGV and AMR is the controllability. Modern AGV suppliers today can provide you a dual-mode option. This will give you the ability to take over your robot and drive it manually, whenever you require and then switch it back to autonomous mode. AMRs can be controlled in terms of their movements however, it will remain autonomous or ‘following human’ options only. Hence, make sure you define your project keeping this flexibility in mind.
Infrastructure Requirements
Many of the AMR demands are driven by the fact that they require zero installation or pre-requisites. With advanced navigation technologies, their tasks are easier to configure and generally follow a free path. However, keep note that modern robotic suppliers are able to extend this technology to AGVs as well. AGVs today use advanced navigation (Eg: SLAM) systems that use real-time location with the existing map created in the system. This eliminates the need for any infrastructure needs and can match the ease of AMR installations. While specific paths need to be defined for pick/drop operations, AGVs today can calculate the best possible route improving efficiency and throughput.
Flexibility
A crucial point to consider is the flexibility of both systems. On ground level, both AGVs and AMRs can offer flexibility in defining your operations. However, an AMR usually works best only if there are large SKUs. Since AMRs mainly function to lessen the travel time and allow operators to focus on other tasks, it relies on the higher number of SKUs to account for noticeable results.
Verdict
AGVs are much more traditional and have years of development under its belt. AMRs can be quicker to install and better for lighter loads. AGVs are robust and cater to the higher and bigger movement of loads. Both solutions have their differences but work for a common goal: automate your warehouse process. Thus, care should be taken while defining a project to select an appropriate solution for you. If you have a wider variety of operations, an AGV is your best bet.
* Note : AGV = Autonomous Guided Vehicles