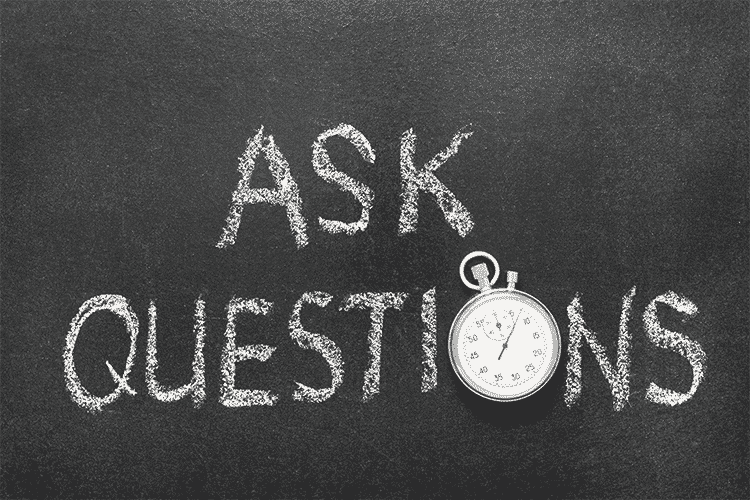
Industries are beginning to uncover the vast potential of robotization. Apart from industrial benefits like increasing productivity, safety, and reliability, they also create tremendous socio-economic value. Robotics, especially AGV providers, can offer flexibility and most of the advanced AGV functionality. Thus, finding an appropriate AGV supplier is imperative. With few key pointers that form the crux of these automation projects, be sure to ask these 5 important questions to your AGV supplier/s.
1. Scalability
When you are looking to automate your warehouse or plant, you must also consider the future demands and expansion possibilities. Automation has the potential to increase your productivity and operational efficiency, which in turn creates increased demands. Hence, AGV suppliers must have flexible solutions that are not just simple but also scalable to handle these increased needs. Make sure you ask about the ease of scaling up your existing operation in the future.
2. Control
Robots today can mimic most of the operator tasks and functions. With a cobotics approach, plants are delegating the repetitive and low value-added tasks to robots, while asking operators to lead due to their expertise, decision making, and even guide in emergency situations. Having the possibility to control your robots, should and when they require, gives the operators an increased level of control and reliability.
Hint: Operator control or dual-mode as its called is beneficial but only if it is easier to switch between autonomy and manual modes.
3. Commitment to safety
With high levels of automation comes increased requirements of safety standards. In addition to strictly adhering to local safety standards, additional functionality is expected to ensure both goods and operator safety. Are the AGVS protected against system failure? Are there sensors to prevent operator safety? If yes, at what level? What are the additional safety systems they deploy to prevent the safe handling of goods?
Did you know? PL-d level safety lasers ensure the probability of failure per hour is less than 0.00001%
4. Maintaining fleet
The process of automation is a continuous one. It means the task is not done just by deploying AGVS. As much as AGVs can learn and develop over time, fleet maintenance is a crucial part of supply chain management. By analyzing data and AGV performance, warehouses can modify their process and extract greater productivity benefits, which is ultimately your goal. Ease of maintenance and data analysis should form a part of your decision making when choosing a supplier.
5. Evidence of expertise
Last but not least, every warehouse or plant looking to deploy a sophisticated system like AGV robots needs to be convinced that the robots are backed by years of industry expertise with pioneering technology. An ideal AGV supplier will have evidence of a fleet of robots running successfully throughout the world. Who are your top customers? Which industries do you currently cater to? By accessing reference customers, you not only mitigate your risks but also potentially helps you keep a tab on industries or regions adopting these practices.
Hint: If your AGV supplier is working with industry leaders or partners to make your robots, chances are that they are already running their fleet successfully in top warehouses across the globe.
* Note : AGV = Autonomous Guided Vehicles