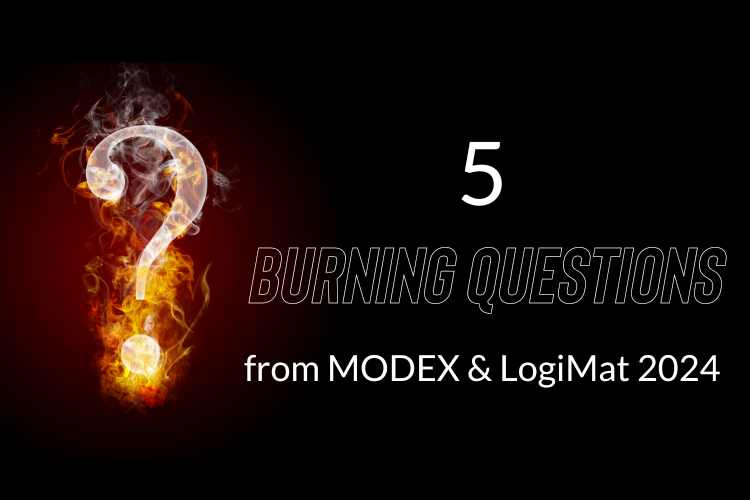
MODEX and LogiMAT 2024, the ultimate gatherings for logistics supply chain professionals, were abuzz with excitement as attendees delved into the world of automation and more specifically Automated Guided Vehicles (AGVs). Despite these events spanning two continents and drawing in close to 100,000 attendees between them, many of the questions BALYO received about AGVs on the show floors shared eerily similar chords.
Amidst the hustle and bustle of the exhibitions, five questions emerged as the most frequently asked, shedding light into the minds of logistics professionals who are looking to embrace the future of material handling.
5 burning questions about AGVs
Is this Robotic Forklift an Autonomous Mobile Robot (AMR) or AGV?
This question continually perplexes logistics and supply chain practitioners and scholars alike. The short answer is, yes.
Today’s AGVs share similar technologies and attributes of AMRs including autonomous movement (e.g. no guide wires or reflectors), integration with ERP/WMS technology to receive orders without human intervention, and working around the clock. And yes, both of these units are robots.
The answer starts to get tricky though when you look at the agility of the two vehicle types. AMRs can usually move around objects with a fleet footed deftness. They are carrying light loads that won’t cause any danger to humans or the machine if they simply scoot around an obstacle. AGVs are carrying tons of goods, so for very good safety reasons, they stop when they encounter and obstacle and then continue their mission when the obstacle is removed. It’s a question that comes up so often we wrote a blog called The Blurred Lines of AMRs and AGVs if you want a more in-depth answer.
How Do These AGVs Work?
How do these AGVs actually work? At first, we Balyonauts in the booth were surprised that this question came after clarifying the distinction between AGVs and AMRs, but then we remembered that AGVs aren’t exactly a new technology.
However, modern day AGVs are far more advanced than their prehistoric predecessors. In the olden times (around the year 2000), AGV installations were a complex undertaking of digging trenches into floors to house guide wires for automated movement.
Today’s AGVs have replaced the guide wire with 3D LiDAR and Simultaneous Localization and Mapping (SLAM) for truly autonomous movement anywhere around the warehouse. Another technology of yesteryear, the reflectors that allowed the robots to pick/drop pallets from racking have now been replaced by cameras on the mast. Infrastructure free and truly autonomous is the mantra of the modern AGV.
How Long do AGVs Take to Set Up?
In the fast-paced world of logistics and order filling, every second counts. While we can’t speak for every AGV vendor out there, we can say that BALYO is putting a wealth of resources behind making the move from manual pallet movement to fully driverless as simple and fast as possible.
It starts with building our robotic AGVs on standard OEM vehicles from Linde MH and Hyster-Yale Group. This simple difference from custom made AGVs means you can cut almost half a year off production time.
The second way we’re making things easier is with our User Journey processes and technologies. In less than a day we can create a digital twin of your warehouse or manufacturing facility. We then use that map to start building your missions and circuits in our Road Editor tools which will create a complete simulation of your logistics flows.
With this “Know Before You Go” approach to AGV deployment, your robots are ready to roll out and start working when they arrive on site.
How many AGVs Will I Need?
This question is a tricky one and will vary from application to application.
The general rule of thumb is that for every one forklift you have operating you will need 1.5 AGVs to replace them. Now, the next natural question is why? Safety is a paramount concern when integrating AGVs into warehouse environments, particularly in shared workspaces where humans and robots interact.
Because of international standards and regulations, AGVs will often operate at a slightly slower speed than your average manual driver. The only place where this rule doesn’t apply is when moving materials into high elevation racks. In that case, as this video shows, the AGVs can keep pace and even surpass the speed of their human counterparts.
How Much do AGVs Cost?
The simple answer is more than a normal manual forklift. We’ll say you’re looking at an AGV investment through a myopic lens though if your calculations begin and end in the here and now. While an AGV could cost three or four times more than a regular vehicle, your savings over time are exponentially higher.
First, there are no drivers required with an AGV so you immediately save on salaries and benefits. There’s no loss to your productivity because the AGV won’t call out sick or need to leave early. AGVs last longer than a manual forklift since every mission and payload is controlled by an algorithm. With this meticulous approach to material handling, you’re not pushing the robots beyond their ideal operating limits, which in the long-term causes less wear and tear to the vehicle.
Finally, AGVs open you up to new modes of operations. Many potential AGV buyers we spoke with were looking to expand into 3 shift or 24/7 operations. In this case the AGV ROI is undeniable and can be achieved in eighteen months or less.
While MODEX and LOGIMAT might be over for this year, the need for logistics and supply chain professionals to improve their operations is a never-ending journey. What we learned at this year’s events is that AGV interest is growing stronger, but there’s still many myths, misconceptions, and misunderstandings about how transformative AGVS can be in warehouse and manufacturing environments. As AGVs continue to evolve and mature, they are poised to become indispensable assets in the modern warehouse ecosystem, driving efficiency, safety, and productivity to new heights.