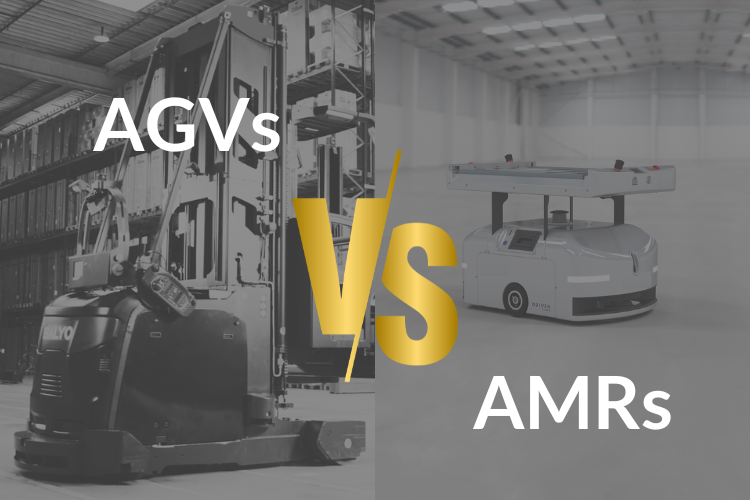
In the dynamic world of warehouse, distribution center and manufacturing automation, two technologies stand out as game-changers:Autonomous Mobile Robots (AMRs) and Automated Guided Vehicles (AGVs).
For years AMRs and AGVs were viewed as two distinct and completely different technologies. The reality is that the lines between these two acronyms have become blurred in recent years. How does one unravel the difference between these two prevalent warehouse and logistics automation technologies? Well, the answer unfortunately is as simple or complex as you want to make it.
Key differences between AGVs and AMRs
Navigation and Autonomy
Autonomous Mobile Robots, as the name suggests, operate independently of human control and involvement, leveraging advanced technologies such as LiDAR, cameras, and sensors to perform repetitive tasks. These robots are equipped with the intelligence to navigate dynamically through their environment, adapt to changes in real-time, and make decisions without relying on fixed paths or infrastructure heavy guidance systems.
AGVs still travel on a fixed path, but the days of relying on magnetic tapes, reflectors, or QR codes on the ceiling for navigation are over. The modern AGV uses the same advanced sensors as AMRs, they simply don’t turn on a dime. This all boils down to physics and safety. AMRs are meant for lightweight loads, transporting widgets and bobbles. AGVs are the workhorses of the warehouse, moving and precariously placing tonnages in weight to points near and far. Physics and safety mandate they move at a measured pace.
Flexibility and Adaptability
AMRs are traditionally renowned for their flexibility. This allows them to effortlessly adapt to changes in the warehouse layout, making them ideal for dynamic environments where the configuration of goods and shelves may vary.
The modern AGV is as equally versatile. It’s simply time to replace the “A” in AGV from automated to autonomous. Today, the greatest barrier in adapting to change lies in the software that controls the robots. However, forward-thinking AGV providers are already developing the tools to reprogram environmental layout changes, circuits, and missions with easy-to-use software.
Collaborative Capabilities
AMRs are designed to collaborate seamlessly with human workers and other machines. Their ability to work alongside humans and share the same workspace sets them apart, creating a harmonious environment where robots and human workers complement each other's strengths.
While AGVs aren’t meant for snuggling or close-quarter collaboration, they certainly don’t need to be cordoned off in a demilitarized zone. Think about a standard forklift. How far away do you need to stay away from the vehicle? A few meters or a couple of feet. That’s the same berth you need to give an AGV. 360° safety sensors act as the new eyes and ears of the robot, ensuring that if anyone or anything gets too close, the vehicle stops and waits for the obstacle to be cleared before resuming its mission.
Real-time Data Exchange
The intelligence of AMRs extends to their communication capabilities. These robots can exchange real-time data with other systems, enhancing overall operational visibility. This connectivity allows for dynamic route planning, optimization of workflows, and efficient responses to changing demands.
AGVs can do the same. Enough said!
Versatility in Task Execution
AMRs are not confined to a single task. They can be easily reprogrammed to perform a variety of material handling activities, from transporting goods between locations to inventory management. This versatility makes them invaluable in warehouses with diverse operational needs.
Being that modern AGVs use the same sensors and internal organs of AMRs, you could use them for tasks like inventory management…but why would you? Just as you could use a hammer to kill a fly, it’s simply not the most efficient use of the tool. Again, AGVs are traditionally large pieces of equipment used for massive tasks of movement and storage. Yes, AMRs can move materials, but only in the smallest amounts.
Choosing Between AMRs and AGVs: Considerations and Applications
Environment Flexibility
The very nature of archaic AGV technology led to the belief that they were inflexible to the rapidity of change that occurs in modern logistics. Nothing could be further than the truth though when discussing modern AGVs. With advanced LiDAR mapping and the right partner by your side, you can change your environment at the speed of business and expect your fleet of AGVs to adapt accordingly.
Anemic or Hefty Applications
Assess the range of applications you need the robotic system to perform. If your need is to move around small parcels or pieces straight to pickers and packagers, then an AMR is where your Google search should be headed. If however, tonnage of materials on pallets is in play, you need to be thinking along the lines of an AGV.
Cobot or not?
Consider the level of collaboration required between robots and human workers. If your operations demand constant interaction and collaboration, the size and maneuverability of AMRs might be what you need. AGVs can work in harmony with humans and be a reliable cobot companion, but a wider berth must be given for safety reasons. As we said earlier, think about how closely you let a normal forklift get to humans and that’s your answer with an AGV.
Infrastructure Investment
We can’t stress this point enough: the modern AGV is no longer an archaic system of wire guides, deep cut trenches into warehouse floors, or oversized QR codes riddled across the manufacturing plant ceiling. With LiDAR for sight and SLAM for navigation memory, today’s AGV is very similar to an AMR in that the navigation all happens onboard the vehicle.
Scalability and Future Adaptation
Think about your long-term needs and the scalability of the chosen robotic system. If your business is likely to undergo changes in production volume, SKU profiles, or facility layout, the modern AGV is just as flexible as any AMR in helping you change.
The Future of AMRs and AGVs in Material Handling: A Convergence of Technologies
As technology advances, the distinctions between AMRs and AGVs are blurred. The future holds the promise of a more integrated and interconnected robotic ecosystem, where these technologies coexist and complement each other. The key lies in understanding the unique strengths of each technology and strategically deploying them based on specific operational needs.
Both AMRs and AGVs contribute significantly to the transformation of material handling processes in manufacturing, warehouses, and logistics. The choice between the two simply depends on the application at hand.