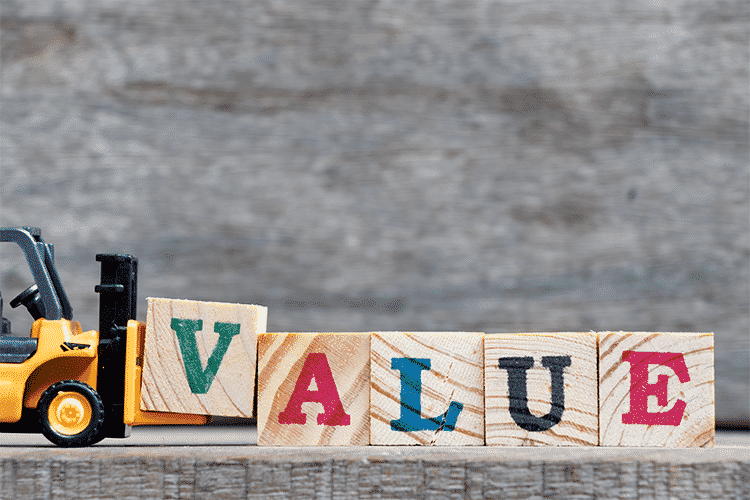
Robotization is one of the most advanced technologies adopted by a warehouse. AGV solutions specialize in providing efficient, faster, and safer operations to your workflow. With a plethora of suppliers today, finding an appropriate solution provider has become one of the most important tasks for any company. We understand that robotic suppliers work on a common goal to simply match your requirements, we at BALYO aim to provide you with a complete load movement solution that is simple and scalable, not just matching your robot requirement. Here’s how we are different.
1. Ease of Installation
The first and foremost aspect a prospective warehouse looks for is, how easy is the installation of robotic solutions? This is where we come into play.
BALYO uses a unique geo-navigation system whereby the movement of the truck is determined by comparing the real-time location (using advanced laser sensors) with the map of the facility programmed before the operation. By using these reference points, our robots maneuver without any additional mode.This means that the installations of BALYO AGVs are infrastructure-free. Hence, you do not need to invest in magnetic stripes, reflectors, etc to deploy an AGV.
Moreover, with a broad portfolio of robots, BALYO solutions are not only simple but also scalable, keeping in mind the rigorous demands of the warehouse.
2. Dual Mode
BALYO provides the customer with a unique platform wherein any operator, should they require, can manually take control of the robots. Once they are done with their operation, they can make the robot revert back to complete autonomy. All this with the touch of a button.
Hence, you can always take control of your robots, should you wish. This provides better ergonomy and operators can further collaborate with these robots to complete the tasks.
3. Industry Expertise
With the execution of more than 130 projects, we have more than 600 robots running worldwide.
We understand the industry challenges and have been constantly elevating the robot functionality to cater to the growing industry needs.
Our robots can be configured exactly as per your requirements and we can provide a customized engineering solution for your plants. What does this mean? Our robots will be unique for your application and the customer, in turn, will not miss out on additional functionality by using a “standard configuration”.
Based on the project definition, we can customize the truck functionality so that the robots are configured for optimum performance. By offering you a flexible and versatile solution, we use our experience and technology to be your ideal supplier.
4. Local and Global Support
Our trucks are based on standard material handling equipment. We work with two of our global partners – Linde Material Handling and Hyster-Yale Group. Any truck with a Driven by BALYO technology is developed in full partnerships with these globally renowned OEMs and are well known to the operators.
By partnering with them, BALYO ensures that the robots are a by-product of years of technical expertise and market research coupled with the advanced technologies of BALYO.
BALYO can deploy robots anywhere in the world and any robot purchased is fully supported by the OEM dealership network with local tech support and local spare parts
5. Safety Systems
Adhering to the strict legislation, all our safety systems are PL-d rated, with a specific sensor loop working independently from the robot software. BALYO also possesses extensive safety know-how which goes beyond simple design, also taking into account all the operations, types of products, to balance performance and safety.
With operator safety of paramount importance, BALYO safety systems are adhering to global safety legislation and ensure that trucks are stopped when detecting an obstacle. Once the detection zone is clear, Driven by BALYO trucks can restart their operations.
Some of the safety systems (not limited to) are :
- Dynamic Cornering Detection:
The robot’s front and rear safety fields adapt to its trajectory, to prevent breakdowns and optimize productivity. - 3D Rack Detection:
A feature guaranteeing the optimum pick/drop of the pallets from high racks, ensuring detection and efficiency. - Anti-push/Drag:
This feature allows a telemeter to measure the distance between the pallet and the backrest, ensuring that the pallets are not pushed or dragged while handling loads with a reach truck.
* Note : AGV = Autonomous Guided Vehicles